5 Factors to Consider When Choosing ProCore® vs. Custom Conveyors
July 11, 2023
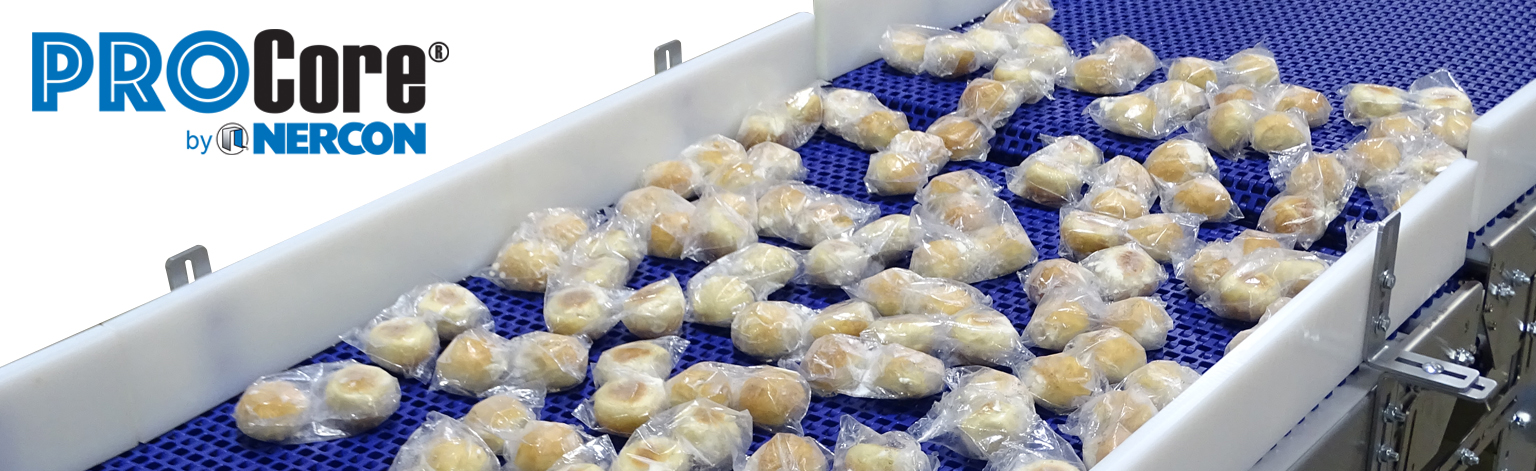
If you’ve ever had to build a conveyor from the ground up, you know there’s some downside. The expense of a custom design. The long lead time required to build it, test it, refine it, and test it again before implementation. Some may think there are downsides to out-of-the-box solutions. Sub-standard quality and less-than-ideal implementations come to mind.
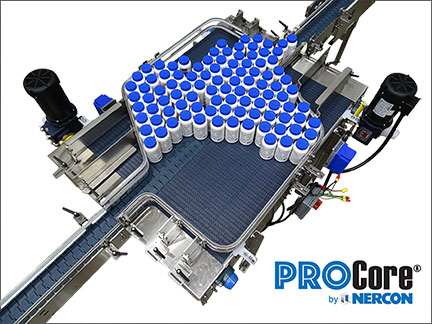
Years ago, our engineering team realized that in many cases, our customers would be better served by a hybrid solution. That was the catalyst for Nercon ProCore®, a family of conveyors that brings together 47 years of conveyor engineering and fabricating experience with modern manufacturing lead times, flexibility, and pricing. ProCore® components are proven to perform. They can be arranged seamlessly to create the right conveyor solution for most manufacturing scenarios. ProCore® also gives manufacturers that require some customization the value of a faster turnaround with proven equipment, without the risk of a ground-up custom build.
“We design conveyors for multiple industries, and that brings an inherent value to ProCore®,” says Darrick Prill, Engineering Manager at Nercon. “Our designs include features that some industries may not have considered but find very useful. At the same time, we’re mindful of streamlined design and use of common parts to keep the price competitive.”
Here are five factors to consider when choosing a ProCore® solution versus a custom conveyor.
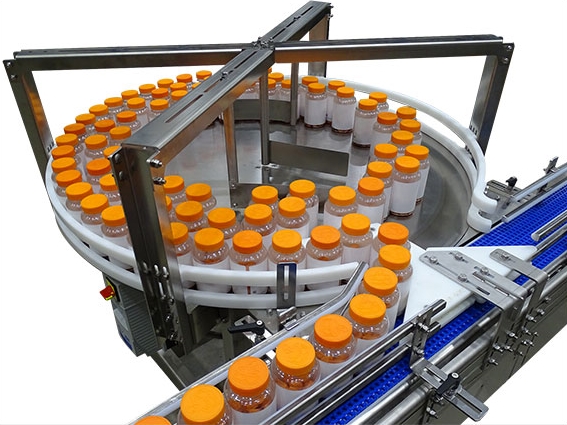
-
Lead time – ProCore® is designed for fast fabrication and delivery. Six to eight weeks is standard. Engineering time is minimal because we’re using proven designs. By manufacturing ProCore® conveyors in our Wisconsin production plant, we can consistently supply them at best-in-class speeds.
-
Price – ProCore® is competitively priced with price points much lower than custom conveyors. We don’t skimp on the materials – the cost savings comes from using proven conveyor designs and common parts.
-
Flexibility – Every ProCore® component is designed for flexibility and works seamlessly with the entire ProCore® family of conveyors, giving manufacturers more options and agility in production line configuration.
-
Less start-up time – ProCore® conveyors are highly engineered by our in-house research and development group and tested extensively. Every component meets Nercon standards for reliability, design, and service before it is made available. That translates into fewer surprises and smoother implementation for faster start-up.
-
Quality – The ProCore® family upholds Nercon's well-known reputation for quality, durability, and performance. On top of that, our conveyor experts consider the entire line, not only the initial challenge, when recommending the solution that will drive the most productivity, efficiency, and uptime.
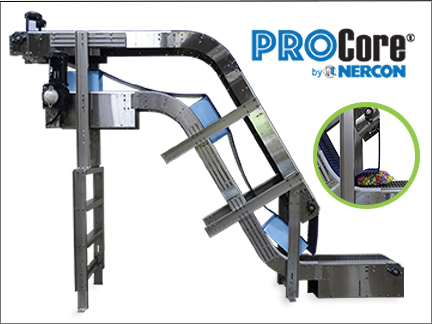
“All of these factors make it very easy for us to stand behind our product,” says Brian Bancroft, Applications Group Manager at Nercon. “We’re with our customers right from the start and beyond installation to ensure our conveyors work as expected.”
“We’ve been doing custom work for four decades and we know that in some cases, custom is still the best solution,” adds Jeff Falash, Research and Development & Field Services Manager at Nercon. “However, we’ve been able to deliver Nercon’s consistently high quality and proven performance much faster and at a lower price point with our ProCore® conveyors. Many times, ProCore® is still the best solution.”
You can see our ProCore® conveyors in operation at PACK EXPO Las Vegas. Stop by booth C-2214 and talk with our ProCore® experts.