Cold Room Manufacturing Challenges
July 09, 2013
It may be hot outside in some parts of the country, but when conveying products in cold temperatures it’s all about keeping it cool. Conveying products in temperatures at or below freezing presents unique challenges to food manufacturers.
Special consideration for conveyor selection begins when the temperature is 32° F and below. In temperatures as low as - 40° F, specifications for conveyors and components need further specialization in order to operate efficiently and effectively. It can be said, therefore, that lower manufacturing temperatures place greater demands on equipment, and warrant more intense scrutiny of purchasing approaches in order to realize the best return on an equipment investment.
Although the same could be said for many areas of a facility’s operation, freezing environments make decisions that balance performance and investment even more critical. This translates to an overwhelming need to understand where a lower-cost roller conveyor option will readily meet a company’s needs, as well as where it could potentially limit production outcomes. Similarly, there’s great value in taking the time to investigate how a more involved investment in a plastic belt conveyor could aid in reducing downtime, improving fulfillment speeds and making the overall work environment more suitable for floor workers, production managers and plant engineering personnel.
Our whitepaper, “Avoiding Pitfalls in Frozen Environment Case Handling Operations” outlines production efficiency, durability, maintenance and safety aspects of roller conveyor systems versus plastic belt conveyor systems in cold room applications.
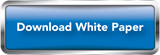