Electrical Controls System Integration Customer Success Stories
June 03, 2021
Nercon’s In-House Electrical Controls Testing Leads to Win for
Two Food Customers
When a $1.5 billion food company needed a new conveyor system for its bottled product, it’s no surprise they turned to Nercon, a leading conveyor systems manufacturer in North America, to handle the design. What they didn’t know at the time was that had they also requested Nercon’s in-house electrical controls solutions at the same time, this would have ultimately resulted in less downtime and hassle in getting the new line up to speed.
Unlike a systems integrator, Nercon designs both the conveyor and conveyor electrical controls system to work hand-in-hand within the larger production line. When designed together, a conveyor and integrated controls system can help streamline customer’s operations and improve production rates—all with minimal labor and commissioning time.
“Nercon provided all conveyors throughout the line for an empty bottle, bottle filling, bottle capping, bottle labeling, bottle case and case palletizing,” said Ben Klubertanz, who’s worked as an Electrical Project Engineer at Nercon for 18 years. “The Nercon controls portion of this project, however, was limited to a 6-lane servo diverter to feed the case packer. The rest of the line integration and controls were provided by a local controls group.”
During the assembly and testing phase at Nercon’s in-house testing facility in Oconto, Wisconsin, the servo diverter was assembled to make the diverter work to its full potential. It was then tested in-house with Nercon's proven controls programming with its specifically designed controls enclosure. Issues were discovered—and resolved—all while at the Nercon facility, stopping future headaches from ever occurring within the client’s production facility.
|
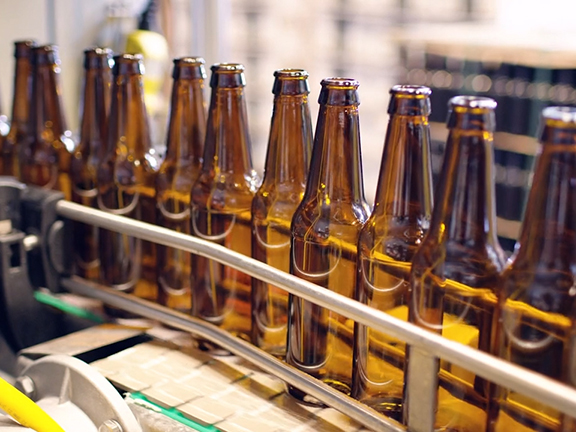 |
The entire conveyor system was assembled at the food customer’s facility. The Nercon diverter was checked out and ready to run after one day of commissioning. Additional time was needed for the rest of the line to work out wiring concerns and design components for the electrical controls that were overlooked by the local controls group.
“When we started to try to run product there were several major issues that arose,” explained Klubertanz. “These were mainly oversights from the local integrator that did not have much experience or thoughts on how to control the line.”
This resulted in numerous sensors and wiring changes for many of the following weeks, ultimately costing the customer added downtime on a new production line. Vendors like the filler, capper, labeler and case-packer had to make multiple trips to the facility to validate their equipment, costing the customer way more than expected for a typical startup.
“In total, the line took about a month to get running at an acceptable speed,” Klubertanz added.
But the giant food company didn’t forget about Nercon’s performance during that start-up. In fact, the project helped shine a spotlight on Nercon’s unique way of approaching electrical controls with its “full system approach.” This resulted in a larger opportunity for the next project.
"The customer was very happy with how our equipment operated on the first project and awarded us the full controls on the next new line for the plant,” Klubertanz said.
Senior electrical design engineer, Kevin Brunmeier, says that when design and programming are done together, Nercon can do things in the design stage that will make programming easier.
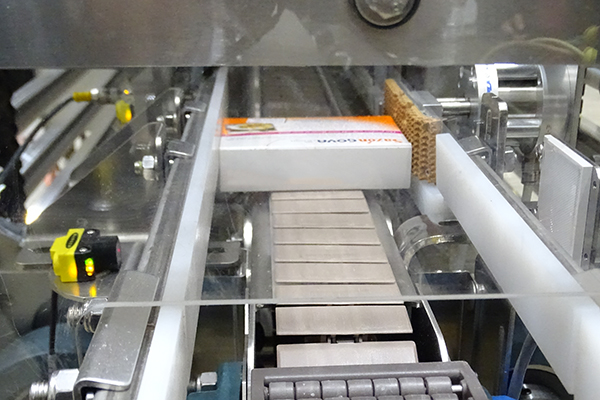 |
“It’s easier to see where sensors are needed and allows us to plan ahead,” he explained. “Those companies who are doing just design but not programming might not think ahead to what will cause a jam or why sensors should be placed in certain places.”
Working closely with the customer and their needs, Nercon was able to provide a controls package and integrate the customer’s needs for the expected line control. The line was assembled and tested at Nercon’s in-house facility just like before and then shipped to the customer’s site for installation and startup.
“The new production line was up and running with all expectations met from the customer within the time frame the customer had for producing a saleable product,” Klubertanz recalled. “The project ran very smoothly with very few changes from the original design. This saved the customer a lot of time and cost with keeping to their start-up schedule.”
|
But this isn’t the only story of cost and time savings Nercon has to tell. When an $8 billion sweet treat manufacturer needed three new production lines built, it turned to Nercon to handle one of them—the largest of the three—entirely designing a new conveyor system and integrating it with Nercon’s electrical controls solution from the start.
“The customer was having a hard time communicating with the other conveyor vendor, so throughout the project design phase, Nercon engineers had weekly meetings directly with the customer discussing the project and areas of concerns,” Klubertanz recalled.
Once all the conveyance issues were resolved, the Nercon controls team began assembly of the controls enclosures.
“A very intuitive and accurate electrical schematic was produced to build these enclosures to a high accuracy with our design standards,” Klubertanz added. “These schematics were also shared with the customer to get quotes for their electrical installation contractor early in the construction phase.”
Equipment was assembled and tested at Nercon’s in-house facility in Oconto once again. On-site, the equipment was installed and wired. The wiring, which consisted of nearly 60 motors and several hundred devices, went smoothly and without any changes.
“We were able to get the line up and running within the allotted commissioning time,” Klubertanz said. “After startup, we received many compliments from the customer and contractors. The other two projects were much smaller but took much longer to get up and running for the other vendor. The other vendor also had very inaccurate schematics and their program was being developed while onsite. Nercon’s proven experience and knowledge of how to control a production line helped keep this customer’s production schedule on time, without costing them any extra time or money.”
A full-system approach, in-house testing capabilities and UL (Underwriter Laboratory) certification all help set Nercon’s electrical controls capabilities apart from its competition. Are you ready for better design and productivity?
Contact us about your next electrical controls project and experience a faster, no-hassle start-up like these customers did!
