Improving Production Efficiency with Re-Flow Accumulation Tables
June 28, 2021
Using Re-Flow Accumulation Tables to Relieve Accumulation Pressure and Improve Changeover Efficiency
It happens every day at consumer packaged goods companies’ production facilities—a downstream pause or backup. The challenge comes in finding a way to accumulate and then recirculate single file products with a consistent product flow to ensure optimum product throughput.
Whether it’s a spilled pint of ice cream, a broken can of soda, a damaged bottle of shampoo or even a planned product changeover, short-term downstream blockages and delays are no stranger in the industry. Finding a way to get back up and running as quickly as possible to improve efficiency is where many companies find themselves spinning their wheels.
That’s where re-flow accumulation tables come in.
Benefits of Nercon’s ProCore® Re-Flow Accumulation Table
With a small footprint and large storage capacity, Nercon’s Re-Flow Accumulation Conveyor Table can accumulate and single file a variety of product sizes and shapes, including bottles, cans, canisters, jars and pucks. Products come into the center of the table and then they recirculate onto two wider conveyors, one that is going the same direction as the incoming line and one that is going the opposite direction.
“The re-flow accumulation table is a versatile unit that handles a nice array of products and provides the needed buffer so customers can keep the filler running,” Jason Gazzana, Nercon Account Manager, said. "It goes in before a labeler or case packer and adds time for the customer to be able to do changeouts without back pressure.”
There’s no gating, no pneumatics, no moving stops or clamps—just simple conveyors and guide rails to circulate products on the table. It can be configured to feed product from the sides and the ends using center lane infeed/discharge or side transfer infeed. It’s best for products that can have product-to-product contact.
“Our re-flow table also has a powered rotating wheel to make all product shapes and sizes work,” Brennan Zenner, Mechanical Project Engineer at Nercon, said. “It doesn’t matter the shape; ovals and non-rounds alike can get orientated in a way that makes it easy for them to get stuck. The powered rotating wheel pulls them out and gets them running back on the line.”
And Nercon has been manufacturing re-flow accumulation tables since 2006, which has led them to change to a lower coefficient of friction variable in their designs, as well as machining changes to bring costs down.
“With minimal electrical controls, it’s built together as one unit to save money on the panel size and amount of work and training needed,” Brian Henshaw, Mechanical Project Engineer at Nercon, said. “We design it so operators really don’t need to worry about it. Once it’s set up and the speeds are dialed in, it just needs to work.”
|
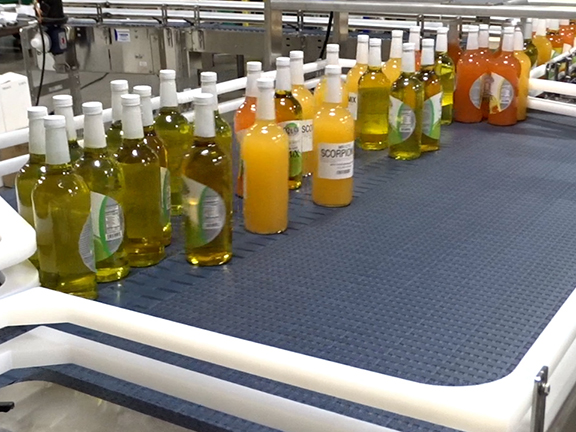
|
A Customized Approach without a “One-of-a-Kind" Price Tag
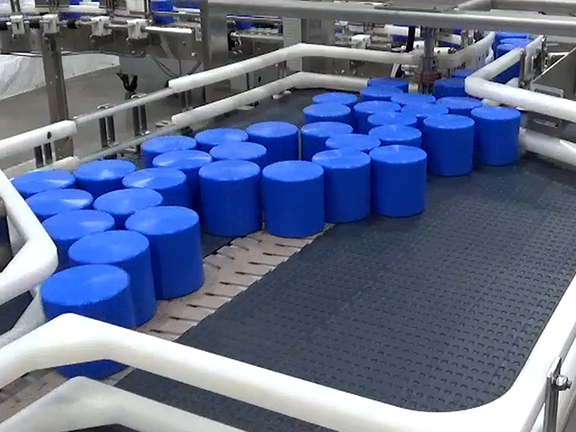
|
When customers contact Nercon for an accumulation table, Nercon’s team of engineers analyzes the application, runs product samples within their in-house production facility in Wisconsin, takes videos at different speeds and sends those to customers.
“We spend a considerable amount of time testing the line and making small tweaks that allow a specific product to run on a re-flow table,” said Darrick Prill, Nercon’s engineering manager. “Because of the experience we have in-house and our ability to test it, we can predict what might go wrong.”
And Nercon stands by its one-year warranty.
“We’re responsible for making sure it functions for our customer,” Prill said. “It’s not advantageous for us or the customer if it doesn’t work, which is another reason we take the time upfront to not only make sure it works, but also look at what issues might arise and make adjustments.”
Packaging and food companies frequently turn to Nercon for help handling non-round products.
|
“CPGs keep throwing curve balls at us, and we love rising to the challenge,” Gazzana said. “Some examples are ketchup bottles, hand soaps and dish soaps, which have so many different shapes and sizes, and with sustainable packaging, the amount of pressure the products can handle is a lot less, which means we make adjustments to meet our customers’ needs.”
Those small adjustments are key to making the re-flow accumulation table work for products with varying levels of product packaging firmness.
“In 2020, we had a customer putting in a hand sanitizer line during the pandemic, so we had them send us sample bottles and we filled them with water since sanitizer was at a premium and put them on our table in our in-house testing facility,” Gazzana said. “We found the bottles were a bit tippy, so we ran the line a little slower. We also found that two re-flow accumulation tables were needed on the line—one before and one after filling. With a minimum footprint, we could keep the sanitiser line going and the customer was very happy with how quickly we delivered a solution to enable them to run multiple bottle sizes on a single line.”
The ProCore® Advantage
Manufactured in its Wisconsin production plant, Nercon’s Re-Flow Accumulation Tables are part of the ProCore® family, meaning it’s part of a pre-engineered line of conveyors. All ProCore® solutions are tested in Nercon’s facilities before they ever make it onto a customer’s production floor to ensure high-quality solutions. ProCore® conveyors are:
- Highly engineered by Nercon’s in-house research and development group
- Designed for flexibility
- Manufactured for quick delivery
- Tested for increased up-time performance
- Competitively priced
- Carefully selected components for reliability, improved design and service
- Equipment can be modified to meet customer preferences
Are you ready to relieve accumulation pressure and improve changeover efficiency?
Contact us for your next accumulation table need and experience the Nercon difference.
