Reduce Downtime due to Upstream or Downstream Backups with Nercon’s Conveyor Accumulation Loop
November 01, 2021
As a tight labor market continues and production speeds and efficiency are threatened, manufacturers are looking for ways to keep product moving and balance product flow, especially when upstream or downstream backups occur.
Accumulation systems keep products moving in critical upstream operations like filling and labeling during downstream stoppages due to equipment consumable material replenishments or malfunctions. Accumulation solutions come in many shapes and sizes to meet the need based on the type and volume of the product and available area for accumulation. The solution must provide the maximum amount of accumulation in the smallest footprint, minimize backpressure, reduce tipping of product and be self-clearing.
Accumulation loops keep upstream equipment producing products while downstream events are slowing or stopped. Some loops consist of two conveyors moving in opposing directions, that, when running create a simple recirculation loop, but are subject to product tipping and best suited to slow product speeds. For increased performance, some designs use a complicated series of multiple side-by-side conveyor chains to create a continuous oval path that increases product stability and throughput but may have limitations in path flexibility and future reconfiguration.
To reduce complexity, a loop created from a single-wide chain reduces maintenance costs but requires large radius turns or dead plates at the transfer points between the conveyors.
The challenge with dead plates is, as the name implies, that they are 4-6 inches of stationary surface in a conveyor system that needs to keep things moving.
That’s where Nercon’s conveyor accumulation loop, with a dynamic transfer section (DTS), comes in.
|
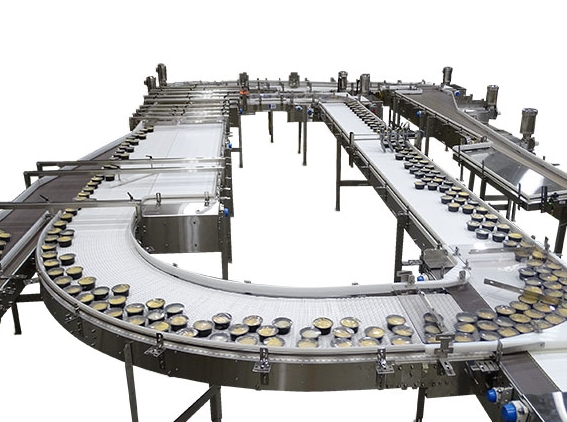
|
Dynamic Transfer Section (DTS) vs. Dead Plates
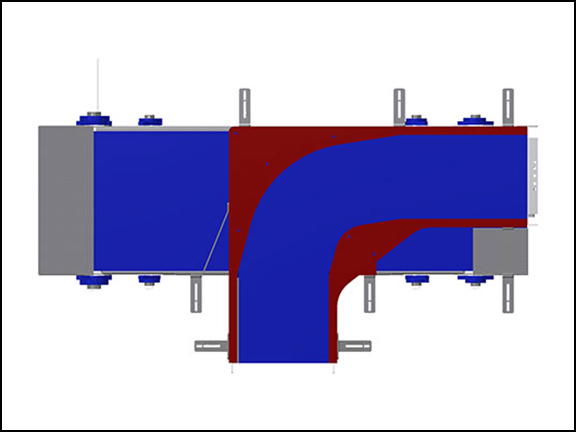
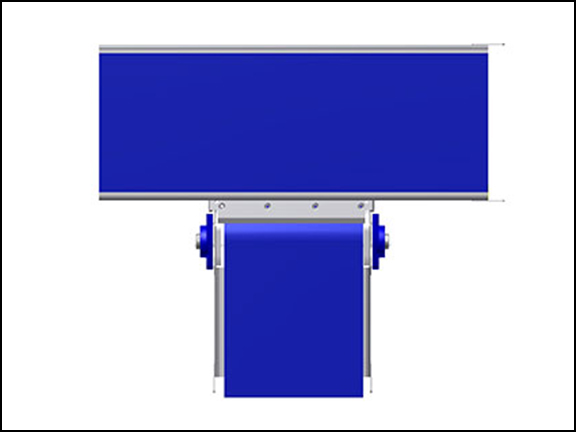
|
“The Dynamic Transfer Section is a specialized self-clearing conveyor turn section that transfers products from one conveyor onto a second conveyor eliminating the potential for any stalled products to be left behind,” explains Nercon President Mike Weickert. “The design incorporates a cantilevered conveyor chain that delivers the product onto the in-feed end of the receiving conveyor with very little gap between. This also increases product stability across the transfer point.”
Nercon’s conveyor accumulation loop is designed to act as a buffer zone for upstream or downstream production efficiencies. The accumulation loop allows the upstream and downstream applications to work independently of each other, creating a helpful buffer zone between processes, thereby preventing congestion.
With minimum backpressure, the accumulation loop helps move a large volume of rigid items that share the same weight and dimensions, minimizing damage on products. With a small footprint and large storage capacity, Nercon’s accumulation loop can accumulate a variety of product sizes and shapes, including bottles, bowls, canisters, cans, cups, jars and rounded trays.
“Our accumulation loop is best for a round product or oval product,” Weickert said. “It’s great for fillers or beverages.”
Like all of Nercon’s ProCore® and HydroCore® conveyor systems, the accumulation loop uses a modular design, which means the system can be custom designed to fit a customer’s needs.
“Our design is based upon a modular concept that allows us to design an accumulation system to fit the clients' available floor space,” Weickert added. “The design has generated a lot of interest. Our expandability and ability to re-configure layouts is unique to the industry.”
|
Benefits of Nercon's Accumulation Loop
Nercon’s accumulation loop features smooth combining, low back pressure, a flexible modular design and low maintenance requirements.
“Because of our DTS turns, there's very little wear in our accumulation loops when compared to a side-flexing conveyor chain/wear strip,” said Weickert. “That means less maintenance and longer lifetime use.”
Three Reasons Nercon’s Accumulation Loop is a Popular Choice:
- Flexibility. Because Nercon’s design is based upon a modular concept, an accumulation system can be designed to fit a customer’s available floor space.
- Simplicity. The DTS design reduces complexity by eliminating stranded products.
- Reliability. Because Nercon’s Accumulation Loop is part of the ProCore® lineup, it is continuously stress-tested and improved upon at Nercon’s manufacturing facility in Oconto, Wis. Additionally, because of its DTS turns, there's very little wear-and-tear compared to an accumulation loop designed with a conveyor chain/wear strip so customers can expect a longer lifetime.
Looking for simple, flexible accumulation solutions you can rely on? Contact us today to discuss a Nercon Accumulation Loop for your production facility.
