Using Armor Starts with Conveyor Controls Integration
November 10, 2011
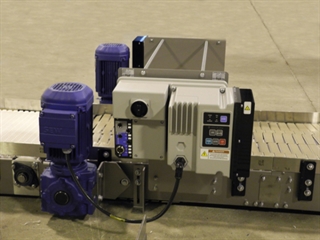
Image description
While Ethernet is simple to use, manufacturers need to consider where it is best utilized when planning facility integration. If all of your control equipment is connected with Ethernet through the switch, you need to understand how that device truly functions.
The traditional proprietary networks required manually setting all node identifications and communication rates, but now Ethernet automatically assigns an address and auto negotiates the baud rate.
However, once a system is running steady state, what happens if something in the control system triggers another ‘auto negotiate’ again? The result would be halting active production at that time, creating more downtime.
While Ethernet is effective in the top levels of the controls architecture, it doesn’t have to be used on the process control and device control levels.
When it comes to the Device Level, there are many options, and planning is required to determine what devices actually need to be on the control network you’re installing.
Adding devices, like variable speed drives, photo-electric sensors and overload relays potentially increase the complexity of your network, but also add significant functionality.
Armor Start products can be deployed without a traditional cabinet; they can still provide individual diagnostics with an LED indicator. Maintenance people prefer a light at the I/O point telling them if the sensor or limit switch changes states. If that operator can provide service without opening the cabinets and suiting up with protective gear, their job is easier and down-time is reduced.