Where’s Your Biggest Bottleneck? (and ways to fix it)
January 29, 2025
Compressed delivery demands and rising operations costs are pushing manufacturers to optimize every aspect of the production process. Still, even in well-designed operations, bottlenecks happen. These are the points where production grinds to a halt, causing delays and driving up costs. In this blog, we’ll break down what causes bottlenecks, how to identify them, and some targeted solutions that will keep production lines running at optimal speed.
Common Causes of Bottlenecks
Bottlenecks occur when one part of the process cannot keep up with the rest, creating a chokepoint that causes downtime and limits overall throughput. Bottlenecks are one type of constraint in manufacturing, but unlike many other constraints, they are typically localized to one part of the process or piece of equipment.
Causes of a bottleneck can include:
- a lot of manual intervention required
- shutdowns to do a regular task like product changeover
- downstream equipment does not run fast enough to clear buffer zones
- changes in products/specifications without appropriate adjustments to the line
- unplanned delays such as an incorrectly oriented package jamming in a wrapper
Identifying Bottlenecks
You can spot bottlenecks on the line in several ways. Work backlogs, products piling up, and unoccupied machine operators are clear indicators. Some of the hidden indicators can include a machine that’s outpaced by the rest of the line, and a machine that requires frequent unplanned maintenance. For manufacturers that track performance metrics, the parts of the process with the lowest efficiency based on throughput, cycle time and capacity utilization can indicate a bottleneck.
Targeted Solutions
Buffering is a proven solution for managing differences in production rates or machine speeds in order to eliminate bottlenecks. It’s accomplished by temporarily storing or holding items in a specific area on the conveyor system. Accumulation solutions help with buffering by holding products in a temporary, stationary space off the production line.
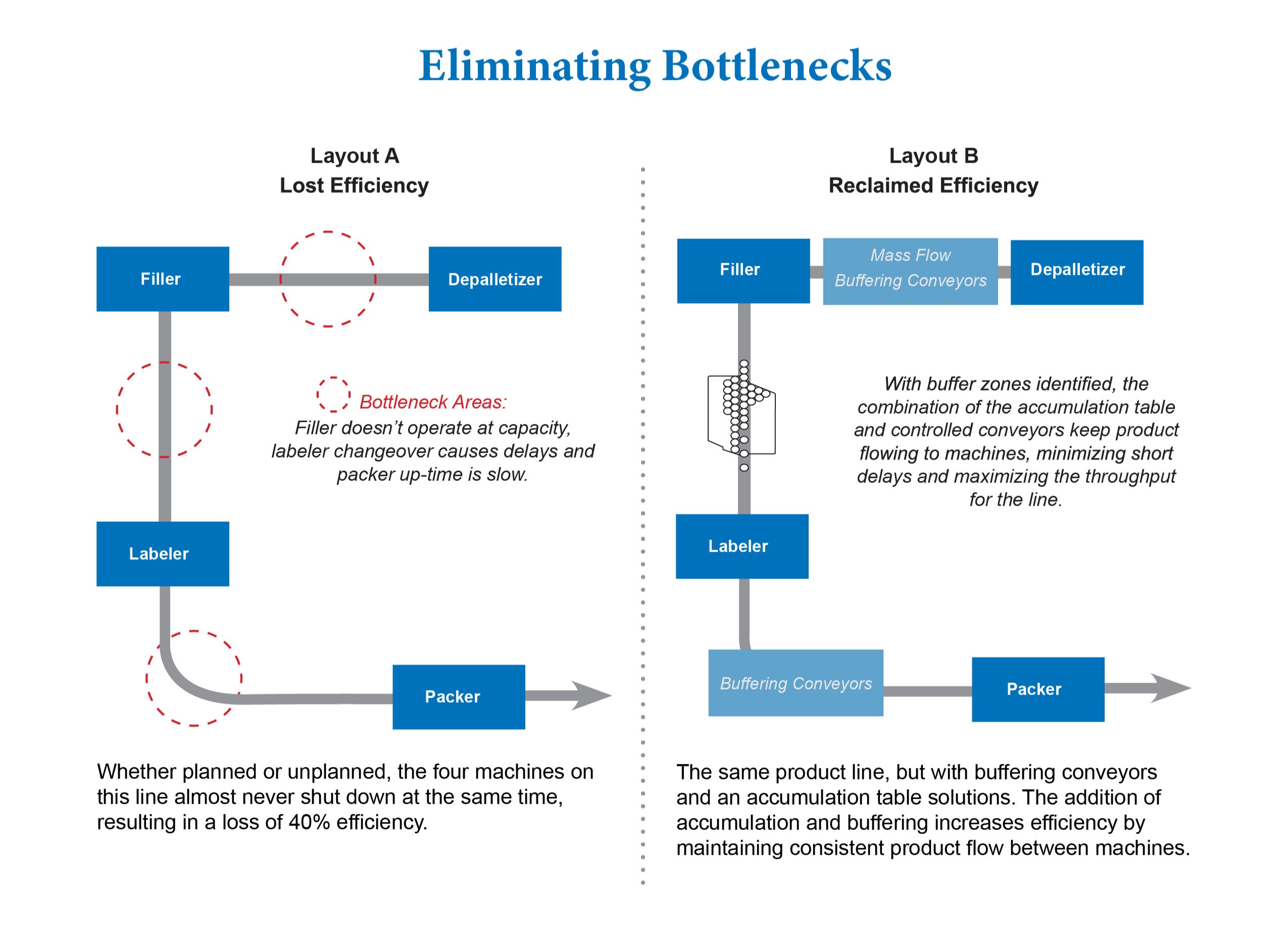
Mass Flow Conveyors accumulate products between machines to prevent buildup of excessive line pressure. The conveyor system accelerates or decelerates depending on demand from downstream equipment.
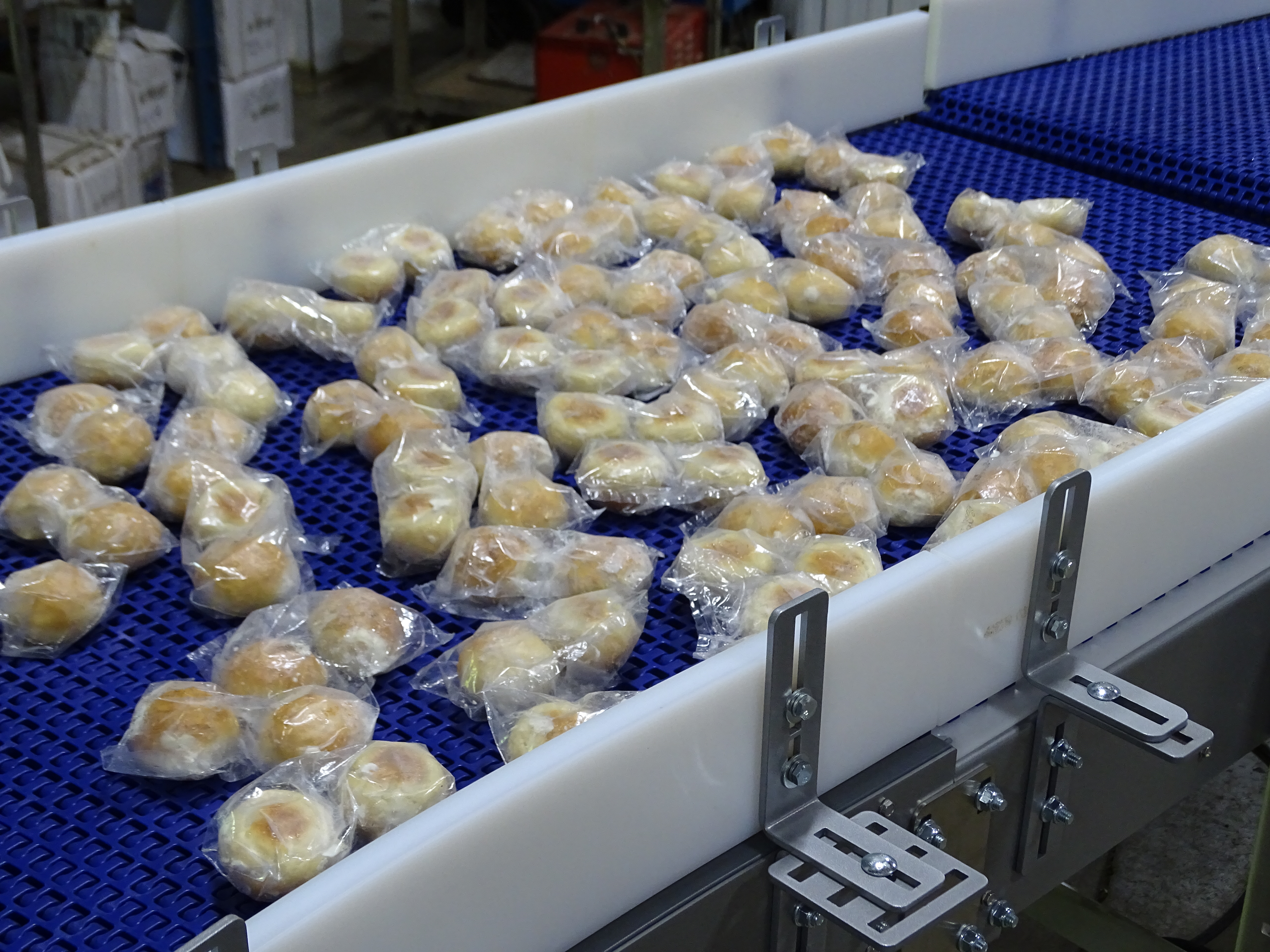
MatTop conveyors offer high flexibility with line layout and can be used as a buffering solution.
Accumulation Tables also temporarily store and manage product flow. This re-flow accumulation table utilizes a recirculating design that relieves back pressure, allowing for smooth, jam-free single filing of products through the discharge. Other types of accumulation tables include the bi-directional accumulation table and rotary accumulation table.
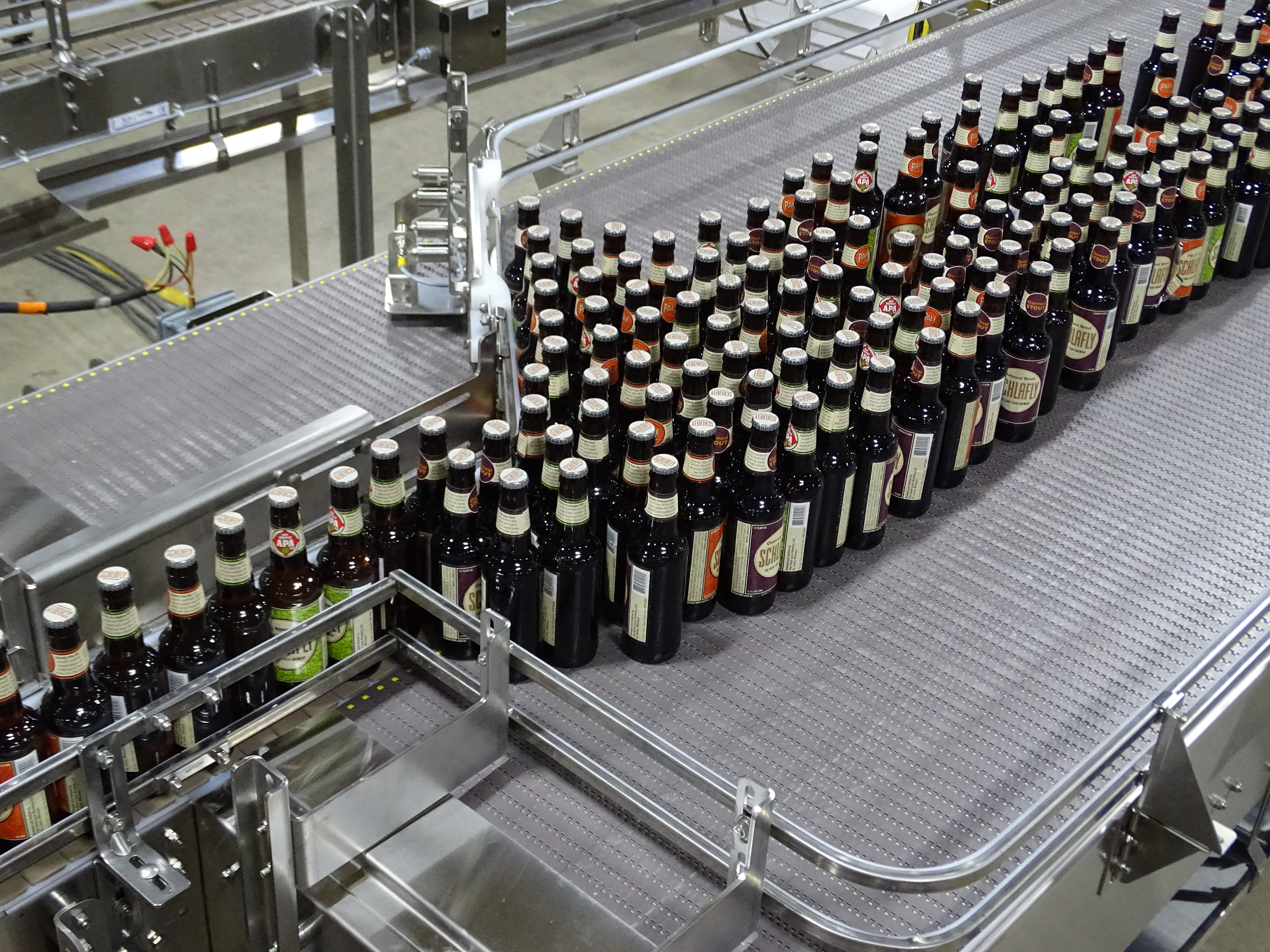
The Re-Flow Accumulation Table can be positioned in key locations to create consistent product flow and optimum product throughput.
How to Resolve Bottlenecks on Your Line
If you have a bottleneck or potential bottleneck areas on your line, Nercon can help. We offer a full range of accumulation solutions. Our conveyor experts have decades of experience evaluating product flows and solving bottleneck issues. We also offer a full line of high-performance conveyors systems and equipment to help your line reach maximum efficiency. Give us a call at 844-293-2814 or request a call from one of our experts today.