Best Practices for Drop-In Rails to Increase Changeover Efficiency
August 06, 2013
UHMW drop-in rail systems are a changeover solution that adjusts the guide rail opening by “dropping in” the fixture. In the photo, a best practice to utilizing drop-in rails for several products is to tag them with color-coded and identifying labels.
One of the biggest benefits of “drop in” rails is the extremely close tolerance that is achievable with the CNC machined parts. When these parts are machined and assembled in an expertly engineered fixture, you’ll have repeatable guide rail openings to within a few thousands of an inch.
Drop-in rails systems are typically specially engineered for turns. Guide rail adjustments through turns are more challenging than straight conveyor guide rail adjustments. As a result, some consumer goods manufacturers opt for the drop-in rail system through turns and are very organized and procedure driven to swap out the rails very efficiently.
UHMW drop-in rails are often used in combination with other solutions. Changeover man hours are moderate because the technician needs to retrieve the rails from storage. If there is a substantial quantity of drop-in rails, rolling carts are often utilized for quick access.
Check out our white paper, “Changeover: Conveyor Technology that Cuts Time,” that highlights all kinds of tool-less conveyor options and guide rail systems that are available to reduce changeover time.
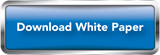